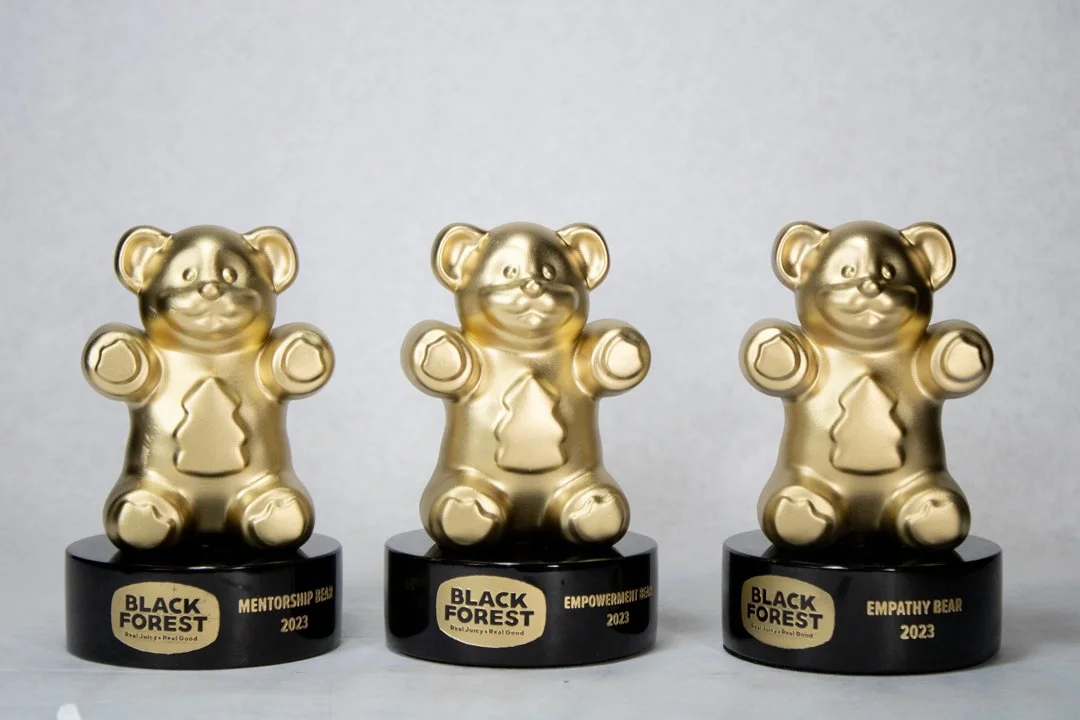
3D PRINTING: A NEW APPROACH TO CUSTOM AWARDS
Using 3D Printing as a new approach
to custom awads
3D printing is a production method that is part of a larger methodology called additive manufacturing. 3D printing was once considered a fringe or cost prohibitive practice, but it has now matured and emerged as a mainstream method for creating custom awards.
Bennett Awards was an early adopter of 3D printing technology. We assembled our first 3D printer in 2010, and began using it on some custom awards projects that were ideally suited to the technology at the time. As the technology has matured, we have shifted more and more of our projects to this new method.
With 3D printing, a custom award design is first created using design software. It The design file is then sent to a 3D printer, similar to sending a digital document to a paper printer. The 3D printer then creates an 3D sculpture based on the design file provided. The 3D printer then creates this sculpture, layer by layer, using one of a variety of materials, including nylon, resin, plastic, and wood, as well as a broad array of metal alloys, including steel, titanium, and precious metals. Different designs and design styles are ideally suited to different materials, and one of Bennett Award’s key areas of expertise is selecting a 3D printing material that is the best fit for a specific design.
Below are some of the awards we have created using 3D printing.
These are examples of what you can create as part of your next custom award design project!
3D printing can be used to create custom awards in a few different ways
Model Creation: 3D printing can be used to create original models, which, like hand sculpted models, can then be used for casting awards.
Embedded Objects: 3D printing can be used to create 3D objects which can then be embedded in acrylic blocks. Subsurface engraving remains the most common method to create 3D images that appear to “float” inside a translucent acrylic sculpture, but 3D printed objects can also be embedded in acrylic sculptures to create a similar effect.
Award Creation: 3D printing can be used to directly create final awards. These sculptures are usually created from a durable polymer material and then painted to achieve the desired finish. Recently, however, 3D printing directly in metal has emerged as a viable alternative, and will continue to gain prominence as we move into the future. 3D printed metal awards can be finished in a variety of ways, including polishing, plating, anodizing, and patination.
Key advantages to using 3D printing to produce custom awards are as follows:
Cost: 3D printing can be an economical way of producing custom awards – in some cases, significantly less expensive than fabrication or casting. However, a very high level of quality detail can be achieved using 3D printing, creating an excellent cost/benefit proposition.
Schedule: 3D printing can reduce the time frame required to create custom awards – depending on the project, it can be up to 2X faster than fabrication and 8X faster than casting.
For each custom award design project, based on the design objectives and project details, Bennett Awards will determine the best production methodology for that specific project. 3D printing and additive manufacturing are now viable options that are included in this choice set. One of the advantages of working with Bennett Awards is that we have deep expertise in all of the available production methods, and are not constrained in terms of which one we can recommend and deploy.